
The upgrade to Peterborough Compressor Station was necessary to reduce noise and vibration at the compressor station, enabling uninterrupted operation without the need for an enclosing structure, which could pose risks in the event of a gas leak.
Project Requirements:
Collaboration with Armacell to ensure the functionality of the new insulation system.
Creation of temporary controlled environments to meet product specifications regarding humidity and ambient temperature.
Unique Aspects:
The project marked the first UK implementation of a new system that required bespoke pattern fabrication for each insulation layer, maintaining zero tolerance for application errors.
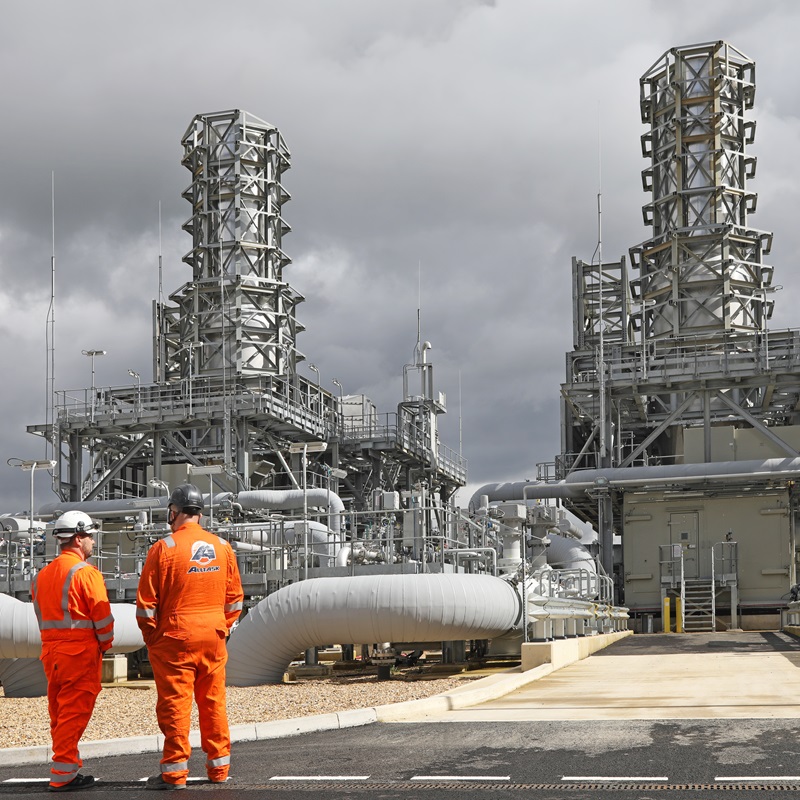
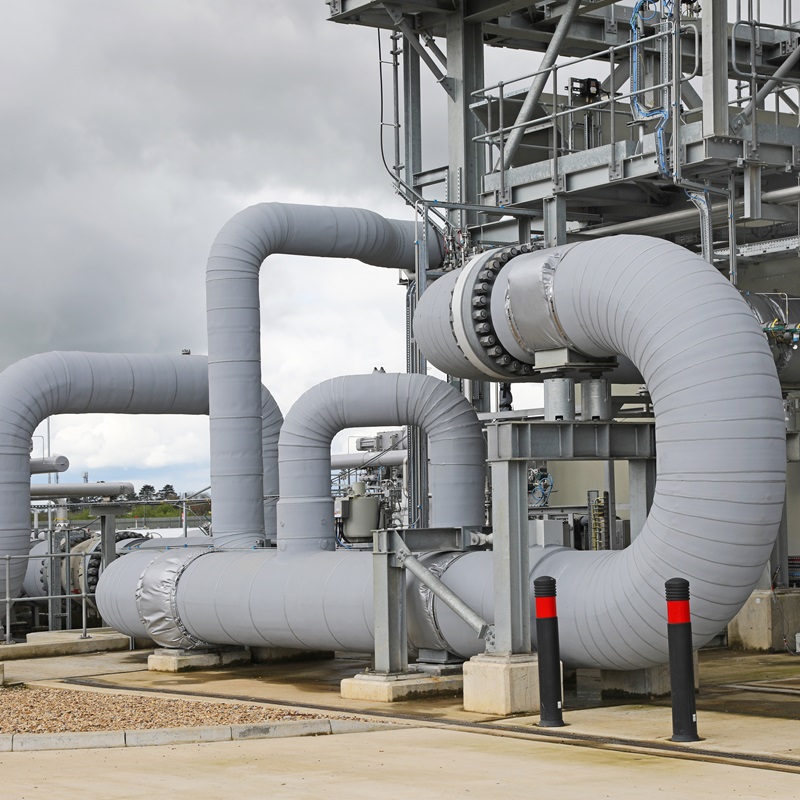
Challenges and Solutions:
Each layer of insulation needed custom fabrication. The project team managed this challenge through detailed planning and precise execution, ensuring flawless adherence to specifications.
Operational Constraints:
Weather conditions impacted the project timeline and processes.
Project Highlights:
The project demanded a high degree of mathematical precision in pattern generation and logistical planning within a live gas compressor station environment. Team members needed specific training and certifications (SCO 91 and EUSR cards) to access the site safely and effectively.
Project Impact:
The Peterborough Compressor Station plays a vital role in the UK’s gas transmission network, particularly for London and the Southeast. The introduction of a Class D 7-layer insulation system has significantly enhanced the station’s resilience against Corrosion Under Insulation (CUI) and effectively mitigated noise pollution.
This project showcased the ability to handle complex, high-stakes infrastructure upgrades with stringent access and design challenges. It emphasized the team’s expertise in managing large-scale projects under challenging conditions.
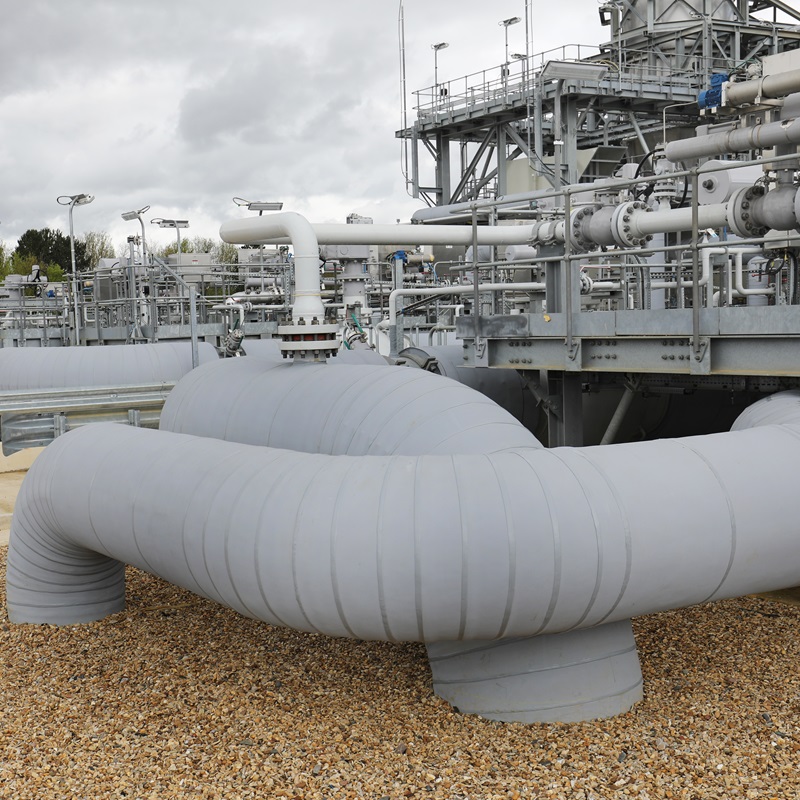
The upgrade of the Peterborough and Huntingdon Compressor Stations has substantially improved the UK’s gas transmission infrastructure. The project underscores the strategic importance and operational significance of these facilities and demonstrates a strong commitment to safety, environmental responsibility, and technical excellence. The successful implementation of this innovative acoustic insulation system represents a significant step toward ensuring a sustainable energy future.
Charlie Griffin-Jones commented, “I’m thrilled to highlight the remarkable craftsmanship of our installers in successfully implementing the Nitrile Rubber’s 7-Layer Class D Acoustic Insulation. Their dedication and skill in managing 138 tonnes across 8 lorries and meticulously fitting over 23,000 square meters truly underscore the excellence of our team.
This project stands as a testament to their expertise and commitment to quality. We will continue to push the boundaries in insulation technology!